60 Years on the Hydrogen Road
“When internal meetings get into decarbonization,” says Rod Christie, Baker Hughes EVP of Industrial & Energy Technology (IET), “through carbon capture, hydrogen, and other programs on the company’s books, the energy level spikes. There’s genuine excitement in the room.”
For a company that built its first hydrogen compressor in 1962, and the first gas turbine in the world to run on 100% hydrogen in 2008, it’s no surprise the employees are excited about the global energy industry now being on board to move forward.
There were a lot of technological hurdles overcome in those 60 years—and there are still many more spanning infrastructure and economics. But there’s finally light at the end of the tunnel thanks to the commitment of countless researchers around the world, and a handful of companies that view hydrogen as a huge opportunity rather than an obstacle.
For Baker Hughes, among those companies there is Air Products.
Air Products chose Baker Hughes for its leading-edge compression and gas turbine offerings and robust hydrogen experience.
In 2021, Air Products and Baker Hughes announced a strategic global collaboration to develop next-generation hydrogen compression to lower the cost of production and accelerate the adoption of hydrogen as a zerocarbon fuel. Baker Hughes contributions include NovaLT™16 turbines and advanced compression technology for the net-zero hydrogen energy complex in Edmonton, Canada, and advanced compression technology for Neom’s carbonfree hydrogen project in Saudi Arabia.
Blue H2 in Western Canada
This project in Edmonton, Alberta, expected to come on stream in 2024, will combine advanced hydrogen reforming technology, carbon capture and storage, and hydrogen-fueled electricity generation to make net-zero possible.
Edmonton’s “blue, but better” hydrogen will replace diesel and natural gas in downstream sectors, providing significant GHG reductions across the region.
Baker Hughes is supplying the project with NovaLT™16 gas turbines. Off the shelf, these units can burn up to 100% vol. hydrogen in WET NOx abatement system and 30% vol. hydrogen in Dry Low NOx (DLN) mode, while design enhancements are moving toward 100% H2 capability also for DLN. NovaLTTM turbines can start with pure hydrogen, with no need of additional fuel for this phase, and can switch, if required, the secondary fuel “on the fly”—not shutting down the plant to move from one gas composition to another.
Also, hydrogen compression will be provided by Baker Hughes’ High Pressure Ratio Compressor (HPRC) technology that enables a significant reduction of compressor bodies due to its unique design and power density. Well proven in natural gas compression, HPRC is now finding a perfect fit in hydrogen applications. The hydrogen recycle service is done through an API618 reciprocating compressor with a single frame capable of managing three different services with different flow rates and pressures.
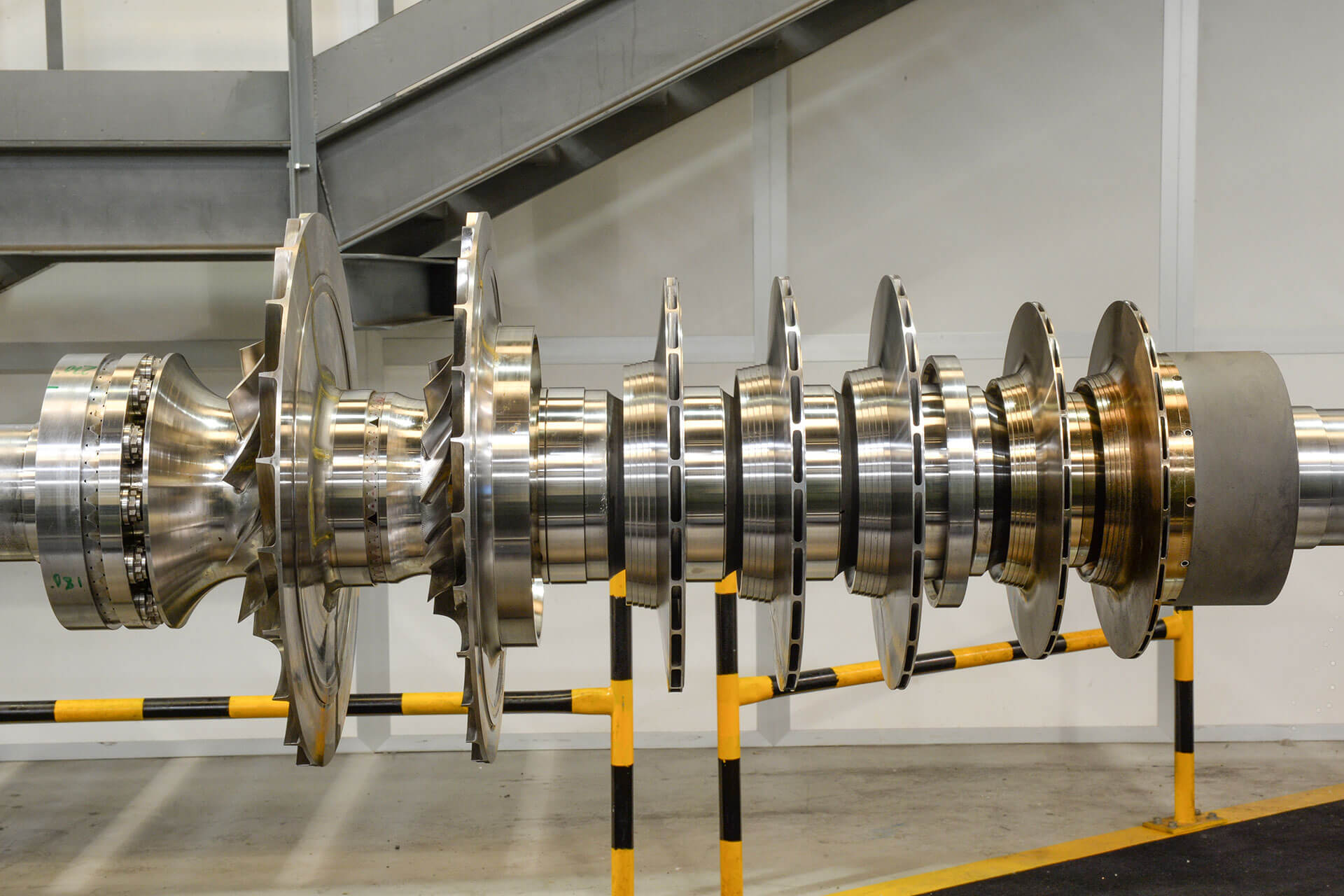
Since the 1960s, Baker Hughes has been designing, manufacturing, testing and installing reciprocating compressors specifically for hydrogen applications, including all related auxiliaries such as cooling consoles, crank-gear lubrication, coolers, and pulsation suppression devices. Hydrogen compression takes place in a 6HG model with six large cylinders, tailored to the required operating conditions and driven by a 9-MW fixed-speed electric motor.
Green H2 in Saudi Arabia
In Saudi Arabia, the NEOM Green Hydrogen project is on track to sell carbon-free green hydrogen by 2026 for green ammonia production, using 120 electrolyzers to split hydrogen from water. When completed, it will be the world’s largest single-line ammonia and the first full-scale green ammonia plant. It will be powered by 4 GW of on-site solar and wind. The fuel will be exported to international markets as green ammonia, which is easier to transport than gaseous hydrogen, where Air Products will convert it back to green hydrogen to fuel the mobility market.
Baker Hughes is supplying advanced compression technology for the production of green ammonia. Compression is performed by a combination of centrifugal HPRC barrel compressors and no-lube reciprocating compressors manufactured. This solution ensures high flexibility in plant operability while optimizing space usage and leverages Baker Hughes’ broad experience and references in supplying syngas and ammonia compressors.
As the energy landscape continues to change, we believe the opportunity to use hydrogen as a zero-emissions fuel source has significant growth potential and as Baker Hughes we can support customers with our expertise and portfolio of solutions in multiple areas along the entire hydrogen value chain.